Checking, adjusting and refitting drive belts
The Video Course teaches you everything about modern cars.
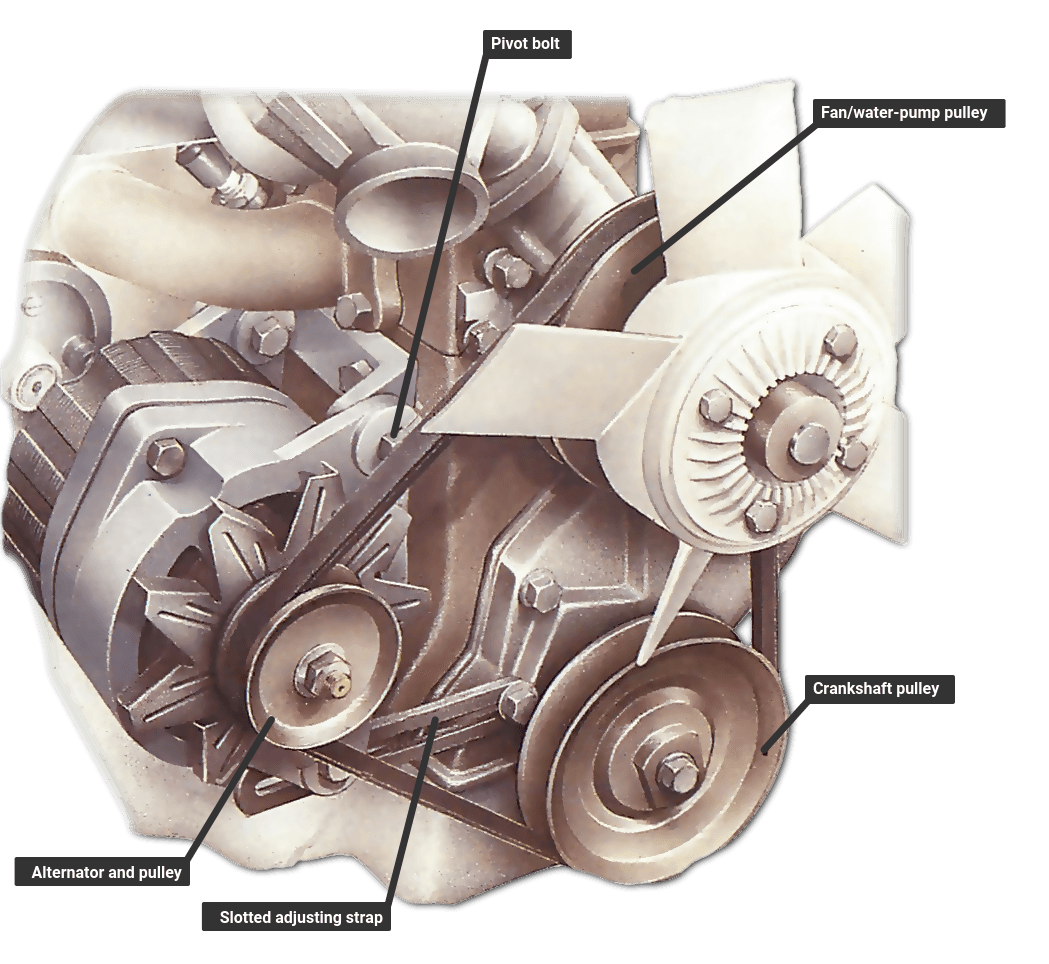
Drive belts always stretch a little in use, because of the strains put on them by driving the water pump and generator , as well as the fan itself if it is in the system. Age and continual flexing also cause belts to crack and deteriorate.
Stretching slackens a belt, so that it slips on the pulleys. A cracked belt will eventually break. The tension and general condition of the belt should therefore be checked at least monthly.
The ignition light comes on to give immediate warning of a broken belt, as the generator stops working.
But the first warning of a slipping belt may well be overheating of the engine or a flat battery — or both.
The belt often starts to slip only when the load on the generator is heavy — for example, when the headlights and rear-window heater are both on — and it becomes more difficult to turn. The fault does not show on the ignition light, but the battery is not getting its full charge and will eventually run down.
Overheating is caused by the slipping belt failing to drive the fan or the water pump properly.
Apart from these effects, a slipping belt is itself worn more rapidly by the heat generated as it slips. The inner face usually cracks first.
A belt that is too tight puts an extra strain on the generator and water-pump bearings , and often causes the premature failure of these bearings.
Before checking a belt always remove the ignition key, to avoid any possibility that the engine might turn over and injure your fingers.
You can make a reasonable check by looking carefully all round the belt, and by feeling around the inner face for damage. To check thoroughly, take off the belt and bend it back a section at a time, so that any cracks there may be are opened and easier to see.
Cracks, scuffs, tears and bumps anywhere on the belt mean that it must be replaced. The Vs of the pulleys in which it runs should also be examined, to make sure they are not the cause of the damage. They must be clean, smooth and free from the slightest distortion, as well as perfectly aligned so that the belt does not suffer from twisting.
Any misalignment is usually caused by mounting the generator wrongly.
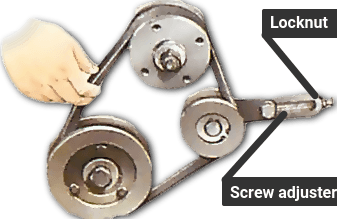
Occasionally a high-pitched squealing sound is made by a belt that is loose or out of line. The sound may vary with the speed of the engine.
Do not try a makeshift cure by lubricating the belt with oil. Doing so will damage the belt and cause it to fail and a belt swollen or sticky with oil may still squeal, even after the original cause has been properly corrected.
A broken belt, though indicated through the ignition light, can still do much damage in a short time.
The flailing ends can tear out electrical cables, cut hoses or even damage the radiator . So switch off the engine as soon as possible if your belt breaks.
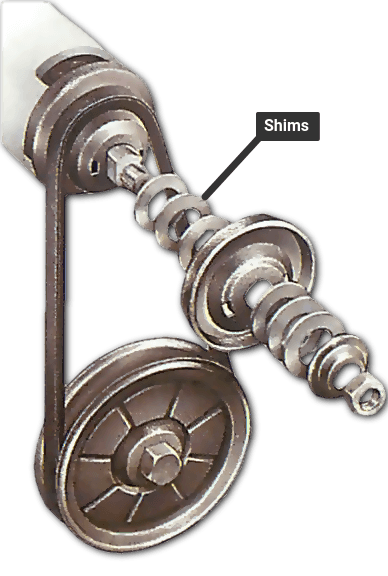
Checking the belt tension
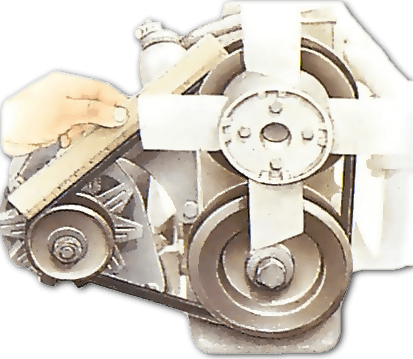
Use a ruler to find the midway point on the belt's longest run between pulleys. Hold the belt between finger and thumb at this point and move it from side to side.
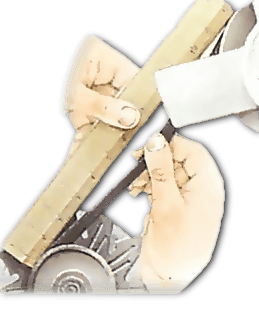
If it moves more than 1/2 in. (13 mm) it is too slack - any less movement and it is too tight. Check the exact deflection recommended in the car handbook.
Adjusting the drive belt
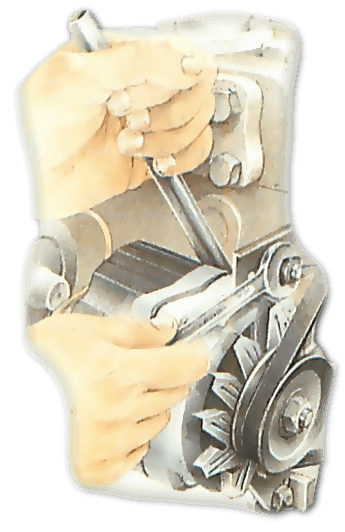
A drive belt is usually tightened or slackened by means of an adjustable pivot where the generator is mounted on the engine.
The generator itself is made to pivot on the two bolts holding it, so that it can swing out and away from the engine. But its movement is governed and can be restrained by a slotted metal strap bolted to the free side of the generator.
Belt adjustment is made by slackening off the pivot bolts, then those on the slotted strap, so that the generator is free to move.
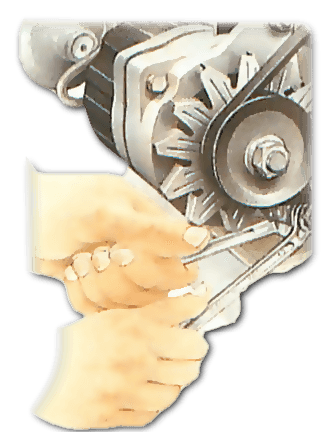
To tighten the belt, use a strong piece of wood to pull the generator away from the engine - a hammer handle will do - while you test the belt tension with the other hand.
When the tension is correct hold the generator firmly in that position and tighten the adjusting strap bolts. Re-check the tension and, if it is still correct, tighten the pivot bolts.
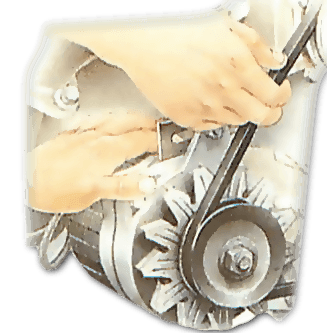
To slacken the belt, loosen the pivot bolts so that the generator is just movable by hand. Move the generator towards the engine a little at a time while feeling the tension on the belt with your other hand.
When the tension is correct, tighten the adjusting strap bolts and the pivot bolt.
Some cars have an idler-wheel pulley which presses on the belt. If yours does, turn the screw adjuster to move the wheel and alter the belt tension. This is often simpler than moving the generator.
Adjusting a split-pulley belt
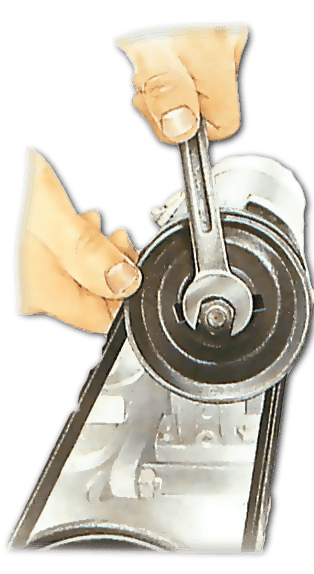
Take off the front half of the pulley and remove or add to the shims between the two halves, so narrowing or widening the V between them.
As the V narrows, the belt is forced further from the centre, up the shoulders of the pulley, and becomes tighter, As it widens, the belt runs closer to the centre and slackens.

Take care not to trap the belt between the two halves of the pulley when tightening them again after adjustment.
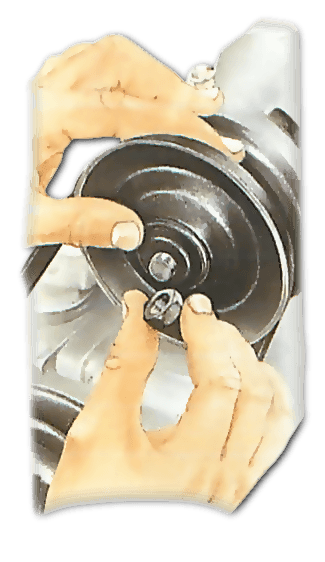
Tighten the nut a little, turn the engine over one-third of a revolution, then tighten a little more, and so on until the halves are firmly clamped together.
Finally, turn the engine over one more time and re-check the belt tension.
Replacing a drive belt
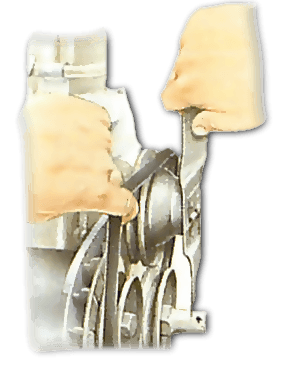
Garages and shops selling fan or drive belts have a list of the correct types for most popular cars. Buy one of the right size and quality.
Belts for alternators are usually made of stronger material than dynamo belts. They are also usually more expensive - but if you use a cheaper dynamo belt to drive an alternator it will probably wear out quickly and perhaps suddenly.
If the correct belt for your car is not on the garage list ask your local dealer for advice, or take the old belt with you for comparison. Even then, make sure the new belt is of the same specification as the old one, or better.
Fitting a new drive belt is usually simple if the pulleys are at the front of the car. But it can be more difficult if the engine is mounted across the car, as on the Mini - because the fan is shroud ed or the belt is otherwise harder to get at. On some cars you must remove the shroud surrounding the cooling fan, or at least part of it.
To take off the old belt, slacken the adjustment bolts on the generator mounting and push the generator in towards the engine as far as it will go.
You should now be able to pull the belt off the topmost pulley - usually that on the water pump. Unhook the belt from the generator and crankshaft pulleys and lift over the fan. On cars with a shrouded fan, it is usually possible to feed the belt out over the blades one at a time, between blade and shroud.
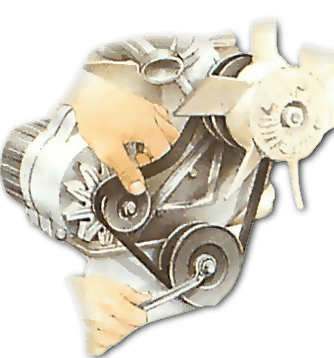
Put on the new belt by the same methods, but in reverse order. Often, however, the belt has to be 'wound' over the top pulley.
To do this, feed it over the fan and on to the lower pulleys, making sure it is properly located in the V of the pulleys. Now stretch it as far as possible over the top one, and wind it on by slowly turning the fan and at the same time pressing it against the pulley rim with your thumb. Take care not to trap your fingers between the belt and pulley.
If your car has an electric or viscous-coupled fan (See How an engine cooling system works ), you may have to turn the engine to wind on the belt, because the fan pulley will not turn the crankshaft pulley and the belt does not wind on.
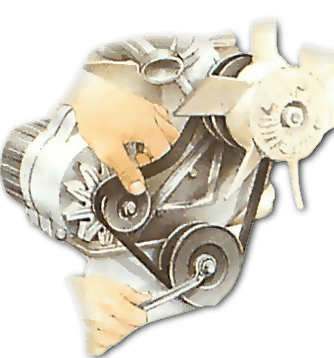
Normally the engine can be turned by using a spanner on the crankshaft pulley.
Do not use a screwdriver or similar tool to lever the belt over the pulley. If the belt is too tight to be fitted by the winding method, it is too small anyway, and you must get one of the proper size.
Remove the old belt on a shim-adjusted pulley in the same way as that used for adjustments. Use all the spacer shims between the pulley discs when fitting a new belt, then remove as many shims as necessary to obtain the correct belt tension.
The Ultimate Car Mechanics video course
Learn everything about modern cars from our new video series.
Learn more >-
We build a Mazda MX5 Miata from scratch
We start by tearing down and then rebuilding the whole car.
-
Every part explained
There's ridiculous detail on every part. Clearly and easily explained.
-
All modeled in 3D
We've created the most detailed 3D model ever produced so we can show you everything working.