Installing a turbocharger
The Video Course teaches you everything about modern cars.
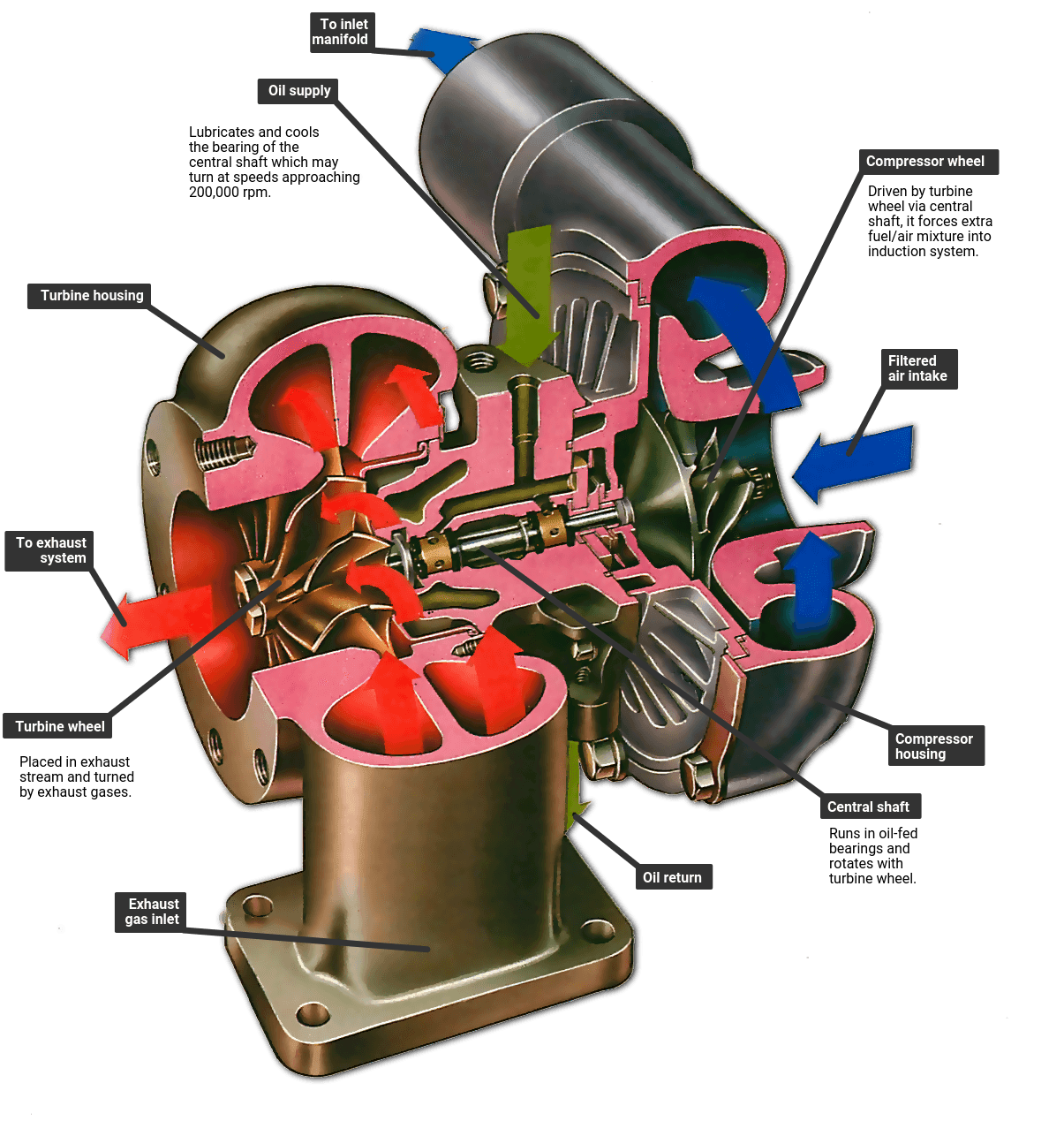
There are two main ways to get more power from a car's engine . The first (and until recently the most popular) is to increase the capacity of the engine. The second is to increase the amount of fuel /air mixture going into the cylinder .
Generally, the more fuel/air mixture going into the cylinders, the more power the engine will produce. So part of the solution is to tune the carburettor , cylinder head and manifolds to allow the engine to `breathe' more freely, but there are limits to how much power can be extracted from an engine by these means while at the same time maintaining the engine's reliability and flexibility.
An alternative way of getting more fuel/air mixture into the cylinders is with a turbocharger .
What is a turbo?
A turbocharger is basically a pump driven by the exhaust gases passing out of the exhaust manifold . The unit consists of a wheel with vanes - the turbine - that fits inside a housing in the exhaust system . From this turbine a short central drive shaft runs to a similar vaned wheel called the compressor that feeds into the engine's air intake.
When the exhaust gases flow
from the engine, they spin the turbine, which in turn spins the drive shaft to turn the compressor. So, when the engine is running, the exhaust gases drive the turbine which makes the compressor pump air into the engine.
A fixed amount of fuel is automatically sucked in with the air if the engine has a carburettor. If the engine has fuel injection , the computer control unit is programmed to suit the boost pressures.
The faster the engine is running, or the larger the throttle opening or both, the faster the turbocharger will spin. The faster the turbo spins, the more pressure, or boost it develops and the more air it forces into the engine to create more power.
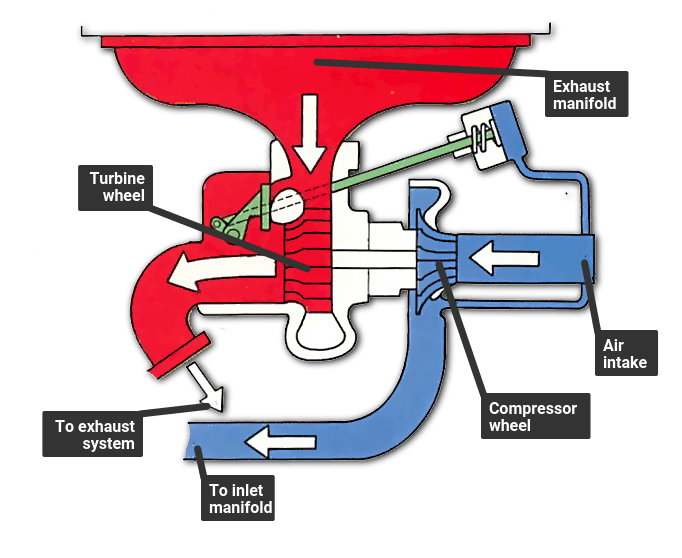
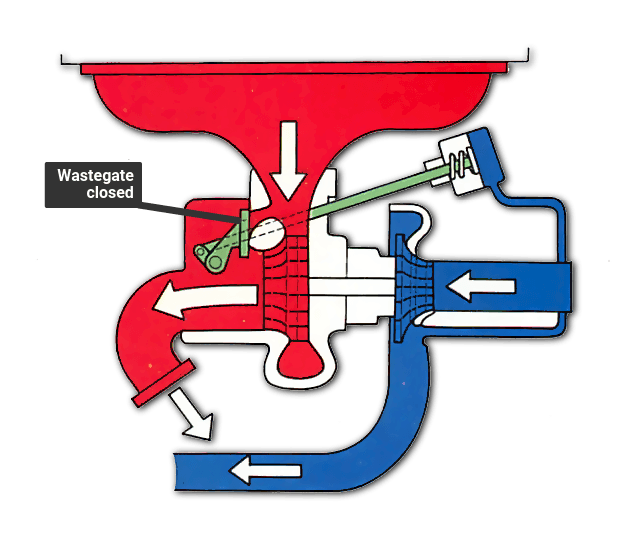
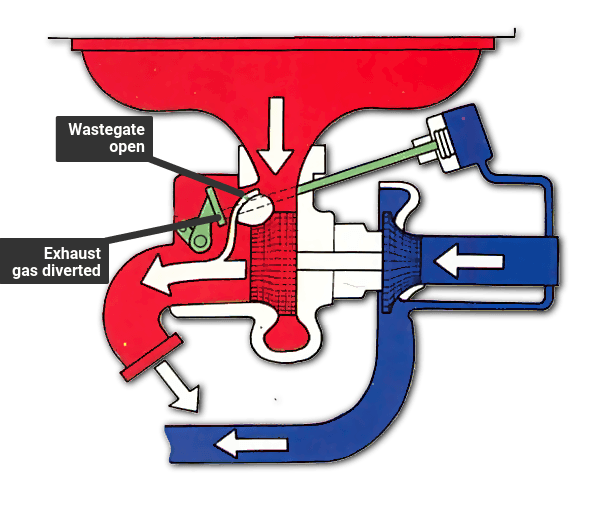
Wastegates
Although the turbo is designed to pressurize the mixture going into the engine, too much pressure would be dangerous because it can lead to 'knocking' (pre-ignition) and put too much strain on the internal components of the engine. Therefore the maximum boost pressure that the turbocharger can produce has to be limited by a valve known as a wastegate.
The wastegate is a relief valve, located in the turbocharger, that opens to let some of the exhaust gases bypass the turbine and flow directly into the exhaust system. If the boost pressure is getting too high, the wastegate is activated by a pressure-sensitive actuator which senses the pressure being produced by the compressor.
Intercoolers
Compressing the air causes problems of its own. When the air is compressed it heats up, which tends to make it expand. Because the purpose of the turbo is to get as much fuel/air mixture into the cylinder as possible, this hot air needs to be cooled down.
To do this, most turbocharged cars are fitted with an intercooler. This looks like a small radiator , and cools the compressed air that leaves the turbocharger. As the air cools down, its volume shrinks, so the amount of fuel/air mixture fed to the engine - and hence the power output - increases.
Installation
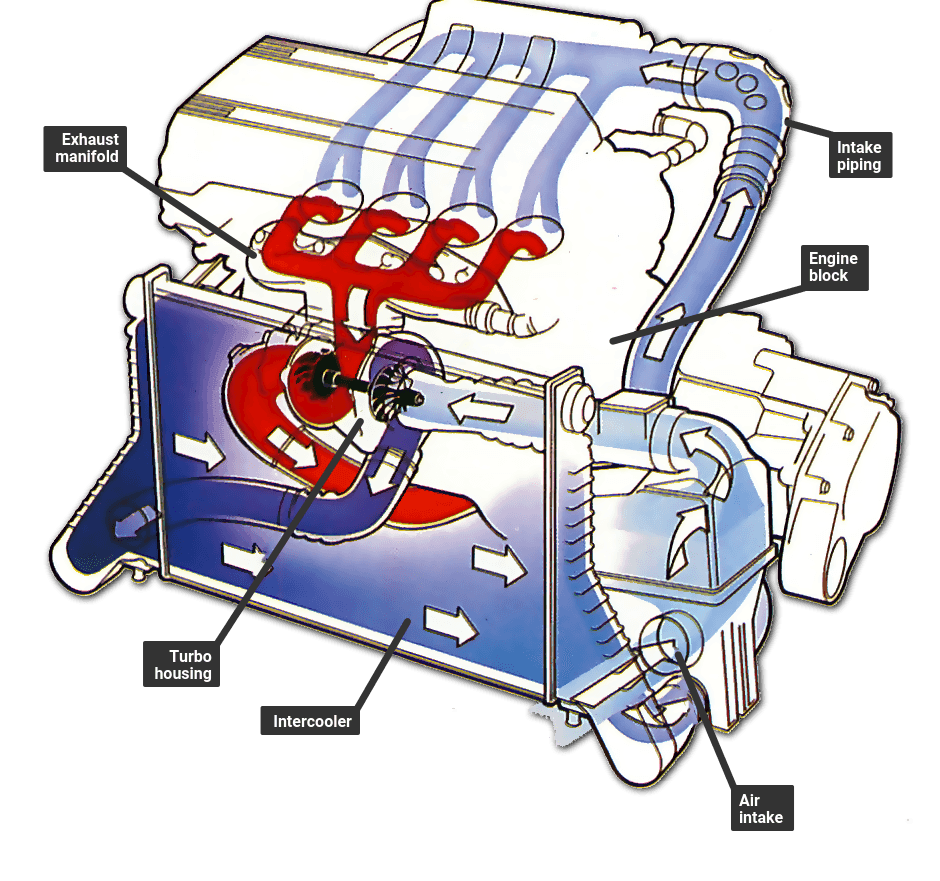
The turbo unit is plumbed in to the exhaust system as near to the engine as possible. This helps to keep it compact and also helps prevent turbo lag. If there was a long length of exhaust pipe between the engine and the turbo, there would be a time delay between the accelerator being pressed down, the engine speed increasing, and the turbo accelerating. The effect would be like having an elastic throttle cable.
Therefore, the turbo is often bolted directly on to the exhaust manifold. The exhaust outlet is in the centre of the turbine housing and leads off to the exhaust pipe.
On the inlet side, the pressurized air leaves the compressor housing via a large-bore pipe. This runs through the intercooler (if fitted), and then to the inlet manifold, or occasionally plenum chamber, where the fuel is added by injection before the air enters the engine.
Lubrication
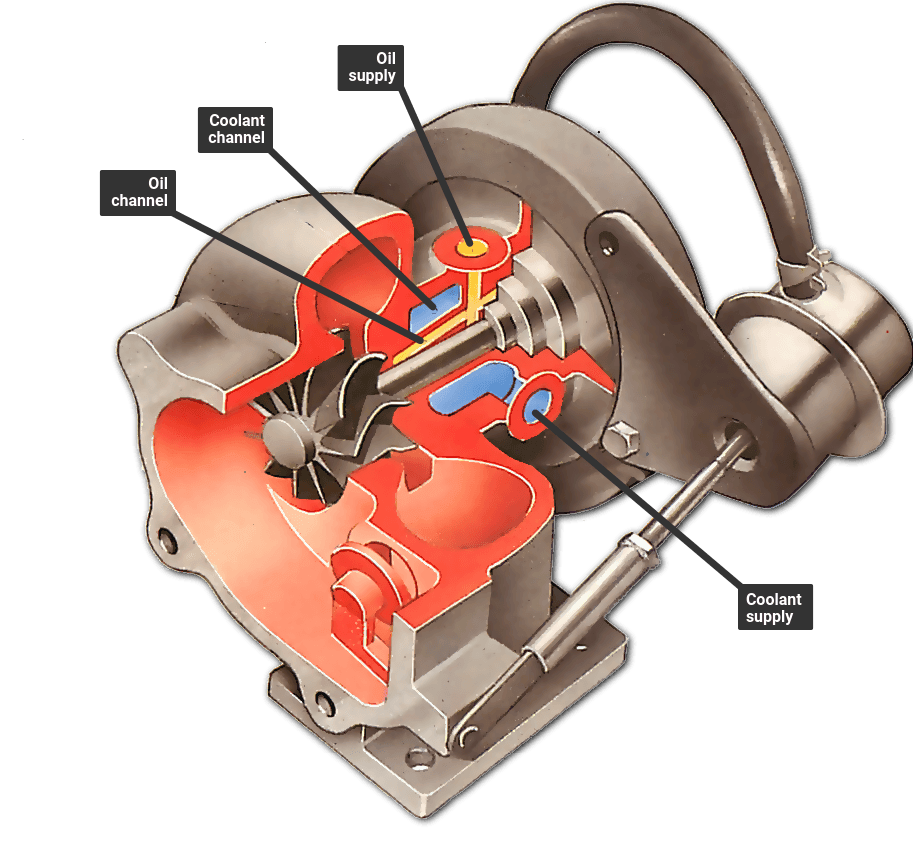
The high speeds at which the turbine can spin create lubrication and cooling problems. In some turbochargers the turbine can spin at up to 200,000rpm, and the hottest parts of the turbo will be at or near the temperature of the exhaust gas about 900°C.
Most turbo units have the central drive shaft bearing fed with oil from the engine. The turbocharger's lubrication system is specially designed to cope with high temperatures.
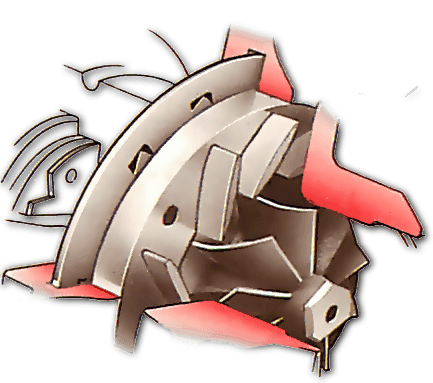
The oil drain pipe is of large diameter to ensure that the oil, which develops a creamy consistency after going through the turbocharger, will drain back to the sump under gravity. If there were a restricted flow in this pipe, it would cause a build-up of pressure around the bearing in the centre housing that would result in oil leaks on the turbocharger.
Some turbos have a water-cooled centre bearing to reduce heat still further. The advantage is that, because the water is still being warmed by the engine, it continues to circulate and take heat away from the bearing for a few minutes after the engine has been stopped.
Refinements
Early criticisms of turbo engines were their poor performance off-boost - when the engine was not turning fast enough to spin the turbine quickly - and the amount of time it took for the turbocharger to start boosting once the accelerator was pressed.
The poor off-boost performance was because road-going turbo engines do not usually have a very high compression ratio . Forcing a lot of pressure into the cylinders is equivalent to raising the compression ratio so, if the engine started with high compression, at high boost the pressures inside the engine could promote detonation problems, or ' knock ', which would result in serious engine damage.
As a rough guide, every three pounds of boost are equivalent to increasing the compression ratio by a factor of one. So if an engine with a compression ratio of 8:1 had a turbo which could deliver nine pounds of boost, the effective compression ratio would be about 11:1. An average family car has a compression ratio of 9:1.
Better engine and turbo control is the answer - almost all turbo systems now use some form of engine management which looks after the electronic ignition and fuel injection systems, retarding the ignition slightly if the engine starts to knock. Saab's APC (Automatic
Performance Control) system goes one step further. Not only does it reduce boost pressure to a safe level, it also allows the engine to be run on any grade of fuel because the management system automatically compensates - although you get the best performance only with the highest grade.
Early turbo engines suffered turbo lag, partly through poor engine management and partly because the lack of suitable turbo units often meant that the engines and turbos were not ideally matched to each other - a large turbo on a small engine will give good top-end power but will lack flexibility. Lag is almost inevitable because a small engine would take time to `spin up' a large turbo unit. A small turbo on a large engine gives good mid-range power with little or no lag, but ultimate power is compromised.
These problems have been minimized by better matching of the turbo and engine sizes, and by using lighter materials such as ceramics and new designs such as variable flow nozzles (see sideline overleaf).
Benefits
The obvious benefit from a turbocharged engine is that of increased performance combined with economy - a turbocharged two-litre engine gives similar performance to an unturbocharged three-litre one, without burning much more fuel than a two-litre.
It's often simpler for a manufacturer to turbocharge an existing engine than to design and develop a new, larger one. Adding a turbo to an engine does not usually significantly increase fuel consumption unless the enhanced performance is used to the full.
The Ultimate Car Mechanics video course
Learn everything about modern cars from our new video series.
Learn more >-
We build a Mazda MX5 Miata from scratch
We start by tearing down and then rebuilding the whole car.
-
Every part explained
There's ridiculous detail on every part. Clearly and easily explained.
-
All modeled in 3D
We've created the most detailed 3D model ever produced so we can show you everything working.