From our insanely detailed guide:
The Valves
We are still working on this article:
Illustrations still needed
Gases flow into and out of the combustion chamber through passages in the cylinder head called ports . This flow of gases is controlled by the valves. There are two sets of valves - one set to control the intake and one set for the exhaust. Valves need to create a minimum of obstruction to the flow of gases when they are open, and create a gas tight seal when they are closed.
On the intake stroke, the intake valve will be open and a mixture of air and fuel can enter. The valve will then close so that the mix can be compressed and burned, then the exhaust valve opens on the exhaust stroke so that the burned mixture can be forced out by the upwards movement of the piston.
The valves are controlled by a camshaft which, at the correct time, pushes each valve open - either directly or through a linkage. The valves must be synchronised with the piston so that they open and close at the correct moment on the piston’s stroke. A timing belt (cambelt in British) or timing chain runs between the crankshaft and the camshaft, binding them together, keeping them locked in sync.
Valve assembly
Early engines experimented with all kinds of valve designs, but for a hundred years or so, car engines have all used the same design: the poppet valve.
Each valve sits in a circular hole formed in the roof of the combustion chamber. When closed, there will be a tight seal between the valve and the surface it presses against, known as the valve seat . The valve is kept closed by the valve spring which pushes up against a disc secured to the valve stem called the retainer .
The pressure forcing exhaust gases out is stronger than the vacuum pulling in air and fuel. It’s easier to blow gases with pressure than to suck them using a vacuum. You can try this yourself breathing through a drinking straw, it takes longer to fill your lungs than to empty them. This means that the exhaust gases move more easily, and so the intake valves are larger (or more numerous) than intake valves to give a greater area for the intake flow.
Valve
The valve itself consists of a circular head connected to a long stem. The stem runs in the valve guide and ensures that the valve is only able to move up and down, and not wiggle from side to side.
The valve is made in two parts and then welded together. The head typically being made form stainless steel, and the stem from high carbon steel. Valves are mostly made from hardened steel, or more exotic materials such as titanium in high performance engines.
When the valve is closed it makes contact with the surface around the perimeter of the valve port. This surface, on which the valve sits, is called the valve seat . The seat must be smooth as it provides a sealing surface, and maximum contact between the valve and seat ensures that the cylinder head is able to absorb heat from the valve. With a cast iron head, the valve seat will be machined directly into the head, whereas for softer aluminium heads, which can’t resist the corrosion of exhaust gases, the valve seat will be made from stronger metal and pressed into the head.
Both intake and exhaust valves get hot during operation. This heat must be dissipated and this heat is mainly conducted across the face of the valve, through the valve seat and into the cylinder head, where it is carried away by the flowing coolant. Heat also makes its way up the stem and through the valve guides into the head. Some performance valve stems are filled with sodium, which melts and sloshes around inside the stem to improve heat transfer.
[Diagram of heat flow in valves]
Exhaust valves have a tougher life than intake valves, they are exposed to greater temperatures because the hot exhaust gases flow around and behind them. They spend their working lives in close contact with hot, corrosive exhaust gases and so are made from extra durable, heat and corrosion resistant materials.
Valve guides
The valves run through a bore in the port, this bore will be lined with a precision milled tube called a valve guide . The valve guide is fitted very closely around the valve stem to prevent any side-to-side movement or wiggling. The tight fit means that the valve face is kept in perfect alignment with the valve seat.
This close clearance prevents oil from leaking into the port, and also helps stop pressurized gases being forced past the valve stem into the cylinder head.
Valve guides are further sealed with a valve stem seal , which is basically an O-ring which seals against the valve stem preventing excess oil and gases from getting through the valve guide into the port. Some oil is desirable in the valve guide to prevent wear and ensure smooth running.
Valve spring
Each valve is held closed by a valve spring . The spring keeps the valve closed, and also keeps the valve assembly in contact with the camshaft or rocker arm when the valve is open. To open the valve, the valve train must push against tension of the spring. The strength of the valve spring is of great importance.
[Valve float illustration]
Too strong and we are wasting power on opening and closing valves, and also increasing wear on the valvetrain. But if the spring is too weak it will fail to close the valve quickly enough at high speeds, the valve will be out of contact with the camshaft in a condition known as valve float which we want to avoid at all times.
The valve spring sits around the valve stem, and pushes upwards on a circular plate called a valve retainer which is locked around the valve stem.
The retainer is locked to the stem through the use of two valve keepers (also known as valve cotters, collets or locks). Valve keepers are tapered and fit into grooves on the valve stem, preventing the retainer from sliding up the stem.
Valve lifters
Valve followers , also referred to as valve lifters or tappets , are cylindrical spacers which sit between the top of the valve stem and the cam lobe or rocker arm. We’ll talk about them in detail in an article on the camshaft.
Camshaft
The function of the valves is very closely related to that of the camshaft and the two act together, with the camshaft controlling the opening and closing of the valves. Read the article on the camshaft for a complete picture of the valve train.
Valve faults
Damaged valves will cause poor compression and serious engine problems. The outcome of valve failure in a single cylinder will fall somewhere on a scale between a non-running engine and poor running - depending on the number of cylinders in the engine.
Valve failure almost always results in a loss of compression in the affected cylinders, due to the failure of a valve to seal the chamber.
Burnt valves
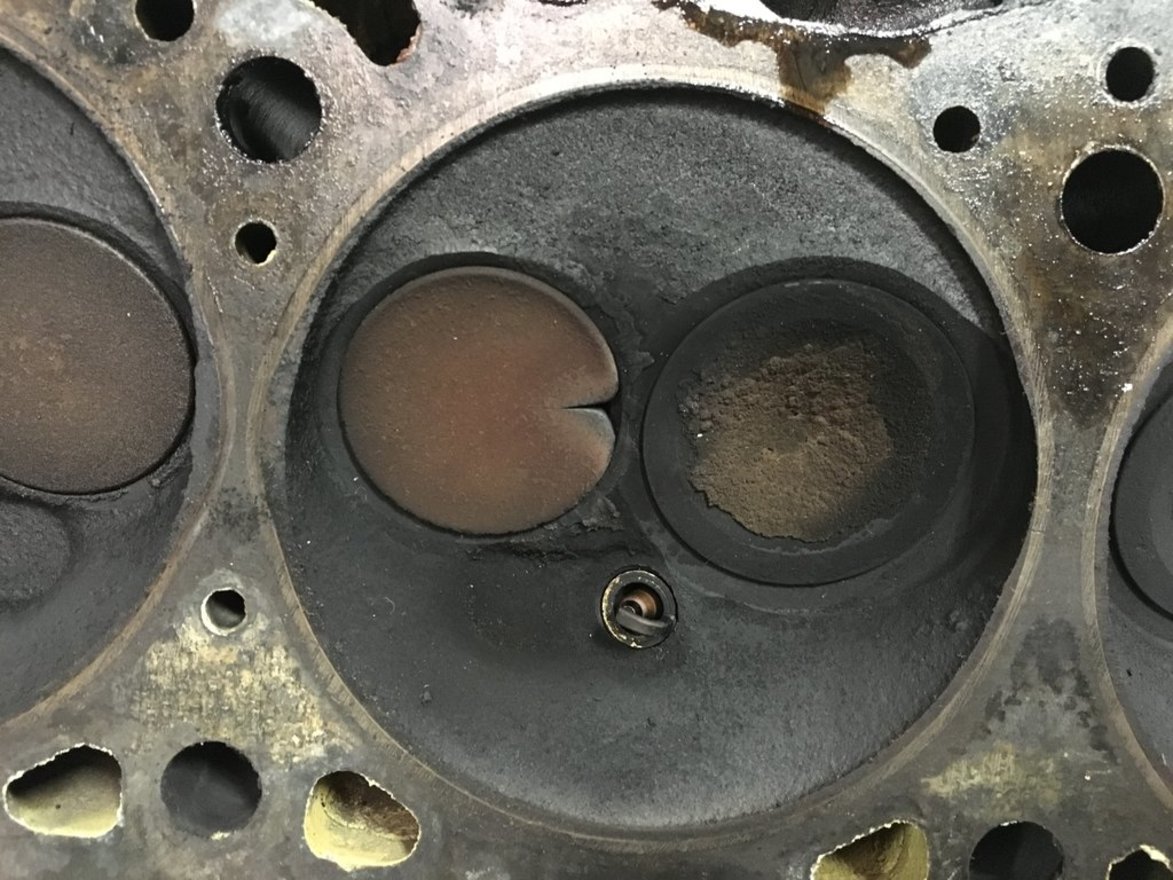
A burnt valve happens when part of the valve face is damaged by heat or corrosion. If the valve doesn’t seat perfectly, either due to being bent or a small crack, then exhaust gases can leak through a small area in the valve. The concentration of gases in this area will tend to eat into the valve head, causing further wear. A burnt valve will cause a poor seal around the valve, resulting in a loss of compression in the cylinder.
Bent valve
The valves are in a constant dance with the pistons, kept in sync via the timing belt or chain. If the timing belt snaps or jumps, then the powerful piston may touch the valve and this will cause a bent valve . An engine where the piston and valve can overlap is known as an interference design - most modern engines are of an interference design . A non-interference engine has a clearance between the piston and valve, even when the valve is fully open and the piston is at the top of its stroke.
Once a valve is bent it will fail to seat properly resulting in poor compression. Depending on the force of the contact between the piston and valve, further damage may be caused to the valve guide.
Continue reading: Camshaft